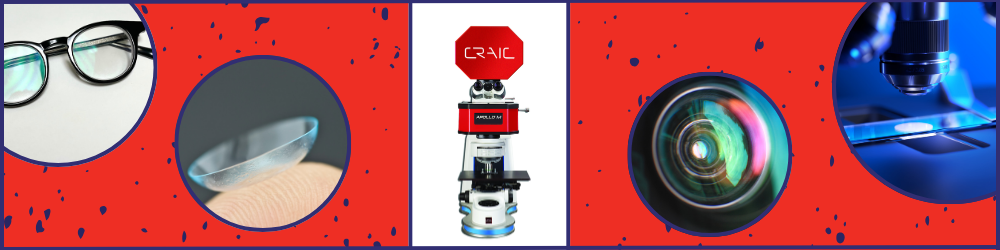
How to characterize antireflection coatings on curved surfaces with microspectroscopy
Curved optical components are central to modern optical systems. They enable wide fields of view, compact lens assemblies, and precise control over light paths. But their geometry introduces a unique challenge: verifying that antireflection (AR) coatings perform consistently across the entire surface.
Unlike flat optics, curved surfaces vary in both angle and shape. As the geometry changes, so do the conditions under which light interacts with the coating. This can lead to shifts in reflectance, inconsistencies in thickness, and localized performance deviations that aren’t visible using conventional measurement tools.
Microspectroscopy makes it possible to characterize these coatings in detail. It provides localized spectral and material data, offering a clear view of how the coating behaves at each microscopic point across the surface. With the right microspectrometer, you can move beyond assumptions and measure AR coatings where they matter most — in the form they’re used and under the conditions they face.
What Makes Curved Surfaces Difficult to Characterize
Curved surfaces present challenges that flat substrates do not. Their geometry affects how light interacts with thin-film layers, making coating behavior difficult to predict. As curvature increases:
-
The angle at which light strikes the surface changes continuously, which alters interference conditions.
-
Coating thickness often varies due to the deposition process, especially toward edges and steep contours.
-
Performance becomes spatially dependent, with reflectance and transmission shifting across the optic.
Being able to characterize these coatings requires high spatial resolution, precise spectral data, and non-destructive access to optical and material information. Microspectroscopy, applied through a well-calibrated microspectrometer, is equipped to deliver all three.
A Step-by-Step Approach to Verifying AR Coatings on Curved Surfaces
Characterizing AR coatings on curved surfaces requires more than a single-point measurement. Because curvature introduces variation in angle, thickness, and deposition quality, a systematic approach is needed to capture how coatings perform across the entire surface. Microspectroscopy systems enable this by delivering localized, high-resolution spectral and material data in a non-destructive manner and with micrometer precision, meaning microscopy is perfect for surface-specific coating validation.
1. Stabilize and Align the Surface
Begin with secure, precise mounting. Curved surfaces often require a motorized stage that allows smooth navigation across changing topography. Focus tracking and Z-axis adjustments help maintain optical alignment as the curvature shifts, ensuring reliable microspectroscopy data across the full surface.
2. Choose the Most Suitable Spectroscopy Mode
Select the microspectroscopy mode that aligns with the coating material and the type of performance insight required:
-
UV-Visible-NIR reflectance or transmittance provides measurements of how effectively the coating suppresses reflectance across specific wavelengths and angles. It highlights differences caused by thickness variation or surface shape.
-
Raman microspectroscopy offers chemical and structural identification of the coating layers, detecting material inconsistencies, contamination, or stress.
-
Film thickness measurements are used to determine the thickness of the various coatings used on optics. This is especially useful for quality control in production of such optics.
-
Spectral mapping delivers spatially resolved microspectroscopy data across the entire curved surface. This makes it easy to identify non-uniformity, edge effects, or coating defects. It can be done for transmission, reflectance, Raman and film thickness measurements.
3. Perform Surface Mapping
Follow a mapping path suited to the shape and size of the surface. Radial scans from the center outward reveal how thickness or optical properties shift with curvature. Linear scans help identify angular dependencies. For full coverage, high-density two-dimensional scans can detect asymmetries and spatial performance trends.
4. Extract Performance Metrics from Spectral Data
Use the collected microspectroscopy data to determine critical coating parameters:
- Coating thickness: Calculated from interference fringe patterns.
- Refractive index: Modeled using spectral fits or known materials.
- Minimum reflectance wavelength: Compared against design targets.
- Spectral bandwidth and angular response: Assessed across relevant points on the surface.
Each of these measurements reveals whether the coating performs as intended across the full surface, not just at a flat or central location.
5. Validate Material Stability and Layer Integrity
Material-sensitive techniques like Raman and IR microspectroscopy add depth to your analysis, especially when integrated into a broader microspectroscopy strategy:
- Confirm that the correct materials are present in each layer.
- Identify chemical degradation, moisture uptake, or organic contamination.
- Detect interlayer diffusion or phase changes caused by stress or aging.
Such insights support both quality control and long-term reliability evaluation of the coating under real-use conditions.
How CRAIC Technologies' 2030PV PRO™ Microspectrometer Supports AR Coating Characterization on Curved Surfaces
The 2030PV PRO™ is designed for precise microscale spectral analysis. It supports transmission, reflectance, absorbance, fluorescence, and emission measurements from the deep UV through NIR, making it ideal for evaluating AR coatings across curved surfaces.
Key features include:
- Full spectral range from 200 to 2500 nm
- Spatial resolution down to one micron
- Integrated Raman, linear and circular polarization modules
- 5D Spectral Surface Mapping™, which captures spatial, spectral, and angular performance in one data set.
These microspectroscopy components work together to deliver detailed, accurate information about how AR coatings perform on curved optical elements, enabling engineers and researchers to evaluate functionality under real operating conditions.
Verifying AR Coatings on Curved Surfaces with Confidence
As optical systems become more advanced, so too must the tools we use to evaluate them. Verifying AR coatings on curved surfaces requires precision, adaptability and depth. These are the qualities that microspectroscopy is uniquely positioned to provide. With the 2030PV PRO™ Microspectrometer, researchers and engineers gain the clarity they need to validate performance, refine design, and meet the optical challenges of tomorrow, measuring coatings with the same precision they’re engineered to deliver — an outcome only possible through advanced microspectroscopy.